Our technology for Clean room
Pursuing stable accuracy and high durability
suitable for extremely clean production line
Products to be used in special environment like clean rooms have high requirements for safety
and accuracy.
To this end, advanced cleaning machines and measuring equipment have been introduced
n the production of freebears to test their performance such as durability in many aspects.
For the long-term safe and reliable conveyance, we are constantly working to improve the level of our product manufacturing.
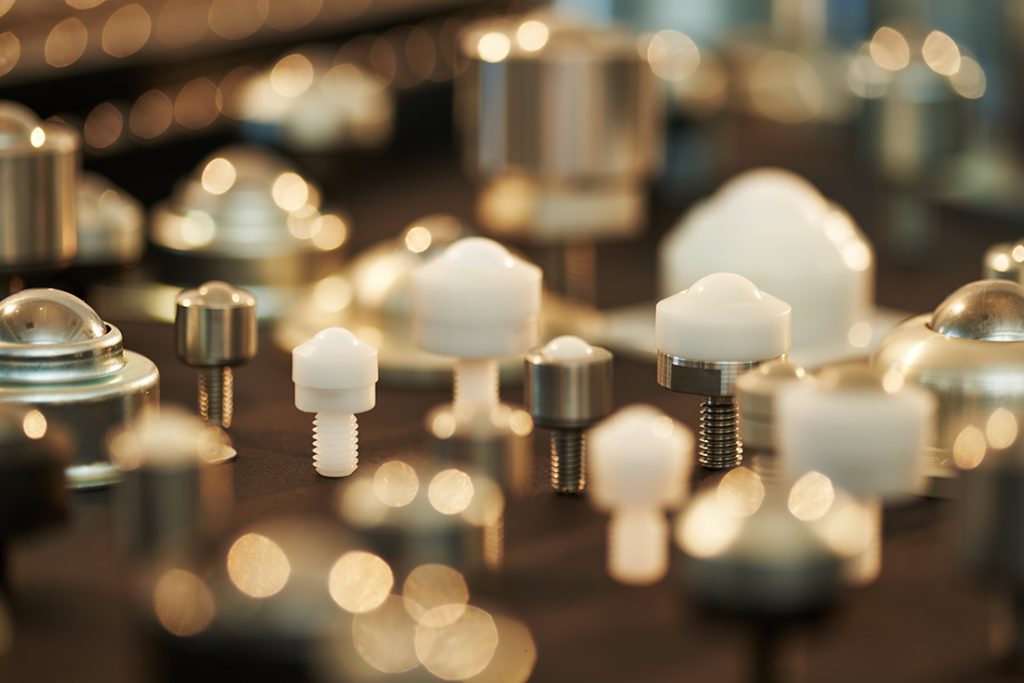
Testing under various assumed conditions
For long-term safe use, we have tested our products under a variety of assumed conditions.
To facilitate the use under various environments and ensure high strength and accuracy, we are constantly striving to improve product quality.
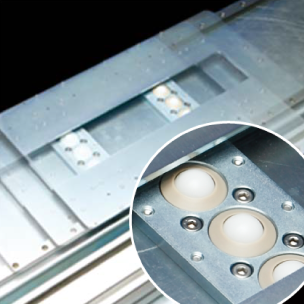
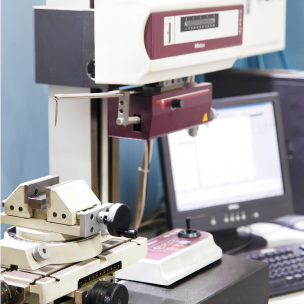
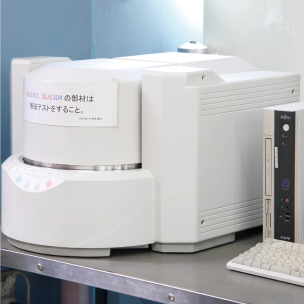
X-Ray Analyzer
Durability test of freebears for clean room
【Test conditions】
① Applied load: 500gf
② Running mode: stroke 15mm (15mm/sec, or 30mm/3sec when reciprocating)
③ Number of tests: 5×106 (measuring 1 time for 5×105 times)
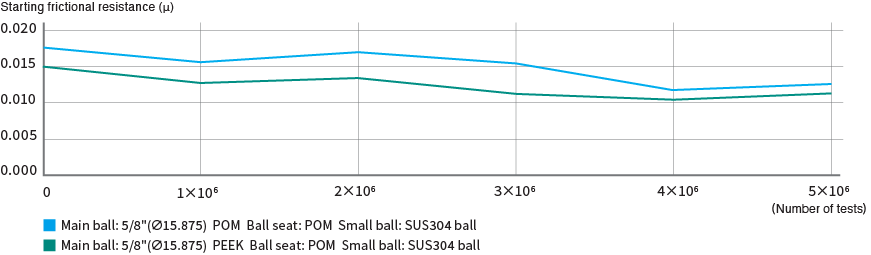
Clean products coming from a clean environment
Freebears for clean room are manufactured in an integrated one-stop system, i.e., every process from assembling
to packaging is performed in the clean room in our factory.
Thus, we can stably provide high quality products.
By adopting the precision washing, customer’s demands for cleanliness can also be reached.
With a wide range of products and careful response, we can meet a variety of applications.
Clean booth, washing room (ultrasonic cleaning machine, vacuum drying machine)
Degreasing and precision washing are performed in the clean booth to meet customer
requirements of cleanliness.
※ Compliant with VOC regulations and standards.
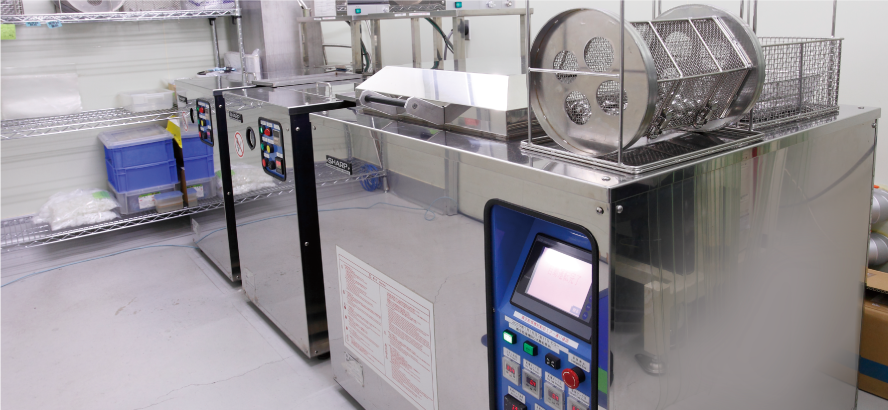
Clean room
The whole process from manufacturing, assembling to
packaging is completed in the clean room, achieving an
in-house integrated production system.
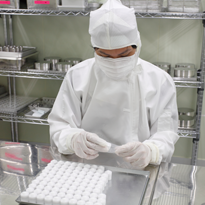
Flow Chart of Degreasing, Precision Washing and Assembling
1. Rough washing for degreasing
Removing oil and grease with hydrocarbon ultrasonic cleaning machine (rough washing).
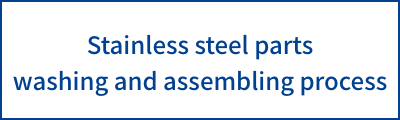
2. Fine washing
Removing oil and grease with a hydrocarbon ultrasonic cleaning machine (fine washing).
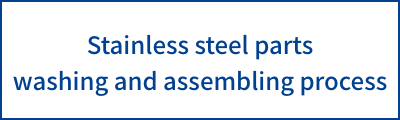
3. Rinsing
Rinsing with hydrocarbon cleaning agent※1。
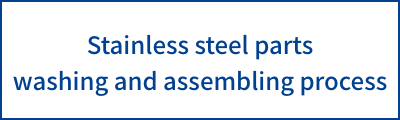
4.Vacuum drying
Using a hydrocarbon vacuum drying machine.
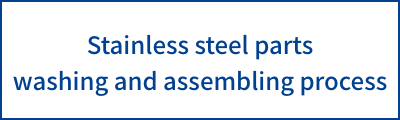
5. Washing for contamination removing
Removing organic dirt (contamination) with a weak alkaline ultrasonic cleaning machine.

6. Rinsing
Rinsing with clean water.

7. Pure water washing
Performing precision washing to remove white residues with a pure water ultrasonic cleaning machine※2
(clean washing).

8. Clean bench
Drying with warm air at the clean bench.

9. Assembling
Assembling under static electricity removal blowing environment in a clean room.

10. Size measuring
Measuring dimensions. Height checking (ball top)

11. Rotation inspection
Performing 100% rotation inspection for freebears. (Visually inspecting white residues at the same time※3.)

12. Clean packaging
Using SBB or CBB clean bags with cleanliness of class 10.

13. Shipping
※1 Hydrocarbon cleaning agent Hydrocarbon ultrasonic cleaning is an environmentally-friendly cleaning method meeting VOC (volatile organic compounds) regulations.
※2 White residues (ion residuals) White traces or marks observed when organic compounds in cleaning agent or clean water are attached to LCD panels or glass substrates.
※3 Visual inspection Visually checking the white residues by moving the freebear on the glass substrate or glass. (It is also applicable to use customer-specified substrates or glass.)
Material Properties
For long-term safe use, we have tested our products under a variety of assumed conditions.
To facilitate the use under various environments and ensure high strength and accuracy, we are constantly striving to improve product quality.
Material name | Wear resistance | Chemical resistance (alkali) | Chemical resistance (acid) | Chemical resistance (ethanol) | Water absorption rate | ※Heat-resistant temperature (reference value) | Volume resistivity Ω・cm |
---|---|---|---|---|---|---|---|
Polyoxymethylene (POM) | ○ | ○ | ▲ | ○ | 0.22 | 90℃ | >1014 |
Ultra high molecular weight polyethylene (UHMWPE) | ◎ | ○ | ▲ | ○ | <0.01 | 80℃ | >1013 |
Polytetrafluoroethylene (PTFE) | ▲ | ○ | ○ | ○ | 0.03 | 260℃ | 1010〜1012 |
Polyether ether ketone (PEEK) | ○ | ◎ | ▲ | ◎ | 0.04 | 240℃ | 1016 |
UPE/static conductive | ◎ | ○ | ▲ | ○ | − | 80℃ | 104 |
PEEK/static conductive | ○ | ◎ | ▲ | ◎ | − | 240℃ | 105〜106 |
※The heat-resistant temperature is the reference value of materials themselves. Temperature settings vary with the operation conditions of freebears.
①Grease is not applied to clean room products. You can also apply a low-dust grease separately. Please contact us for information
on the manufacturer and model.
②Cleanliness C100~C1000 (C100 as standard. If the cleanliness is below the value, please contact us.)
※Cleanliness means that the product is manufactured in a clean room.
③About cleaning See the above flow chart.
④For other materials, please contact us.